Engineered Beauty: Advanced Crafting of Custom Birthstone Necklaces
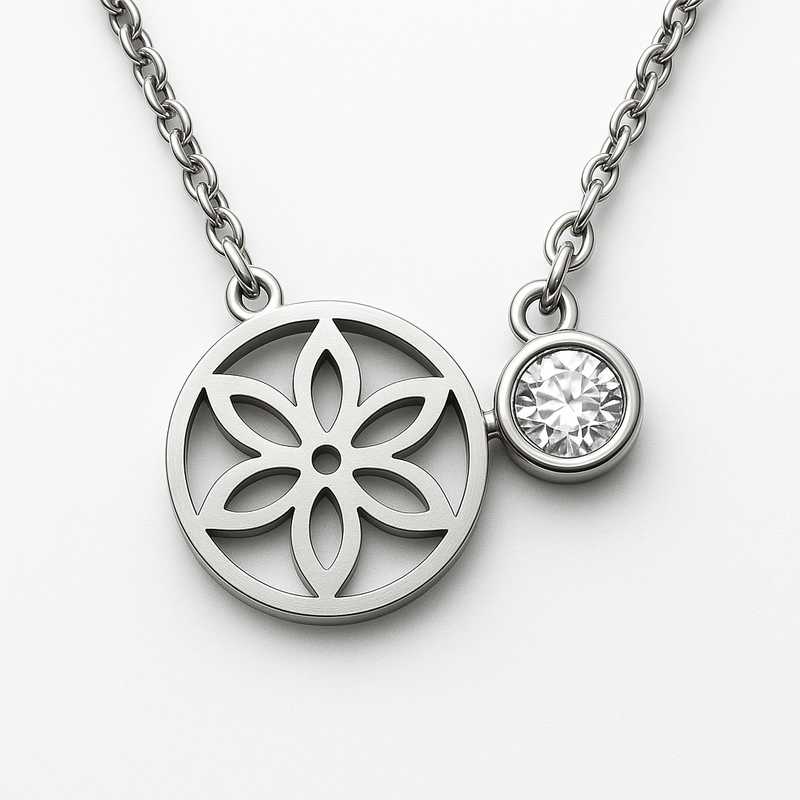
Showcasing 304 vs. 316L stainless steel, precision tech, and green manufacturing for OEM/ODM excellence
In a competitive landscape where both design and durability matter, custom birthstone necklaces have transcended mere accessories to become symbols of precision engineering and aesthetic mastery. For OEM/ODM stainless steel jewelry manufacturers, understanding how materials and technology influence the final product is key to delivering compelling value to B2B customers. “Engineered Beauty” explores how innovative manufacturing techniques, sustainable practices, and the nuanced properties of different stainless steel grades—namely 304 and 316L—drive the future of customized jewelry, particularly birth month flower charm necklaces. This guide is tailored for businesses seeking long-term partnerships and high-performance production for private label or white-label jewelry lines.
Material Matters: 304 vs. 316L Stainless Steel in Custom Jewelry
The foundation of any premium necklace begins with material selection. Two industry standards—304 and 316L stainless steel—each bring distinct properties that affect performance, aesthetics, and end-use scenarios. Understanding these differences is essential for B2B clients selecting materials for their custom charm necklace lines.
Corrosion Resistance and Durability
304 stainless steel is the workhorse of the industry, offering excellent strength, formability, and corrosion resistance under typical environmental conditions. However, when exposed to high chloride or saltwater environments, it may develop rust over time.
By contrast, 316L stainless steel contains molybdenum, a critical alloying element that significantly enhances resistance to chlorides and harsh chemicals. This makes it the go-to choice for jewelry worn daily, in humid climates, or near the sea.
Applications and Market Alignment
- 304 Stainless Steel: Suitable for casual fashion jewelry, occasional-wear accessories, and indoor events like corporate gifting.
- 316L Stainless Steel: Ideal for high-end, heirloom-quality jewelry, fitness and wellness brands, and consumers seeking hypoallergenic and tarnish-resistant pieces.
For OEM/ODM customers, offering both options empowers brands to cater to tiered markets without sacrificing design integrity or manufacturing efficiency.
Precision Manufacturing: Laser Cutting, Hydraulic Forming & Corrosion Patterning
The artistry of a custom birthstone charm necklace is no longer confined to handcrafting. Today’s high-tech approach ensures precision, repeatability, and scalability for large production runs, all while preserving fine design details.
Laser Cutting for Micro-Precision
Laser cutting enables the intricate detailing of birth month flowers, names, and geometric patterns with sub-millimeter accuracy. Its advantages include:
- No tooling required, enabling flexible design changes
- Reduced material waste through optimized nesting algorithms
- Exceptional edge finish, minimizing post-processing needs
OEM case study: A European wellness brand used laser-cut 316L pendants for their chakra-inspired birthstone series, ensuring consistency across 10,000+ units with minimal scrap rates.
Hydraulic Forming for Structural Strength
Hydraulic presses are essential for shaping pendants and bezels without compromising the metal’s grain structure. This method is ideal for forming domed charms or creating subtle 3D effects that elevate a piece’s perceived value. Hydraulic forming reduces micro-fractures, ensuring longevity—especially important for sentimental items like personalized necklaces.
Corrosion Patterning Techniques
Controlled corrosion, via selective etching, allows the creation of natural textures and matte contrasts without paint or coating. These patterns are especially effective in differentiating flower motifs for each birth month. For instance, a March necklace can feature wave-like etching that mirrors aquamarine water, while a December model may incorporate snowflake textures within the pendant frame.
Eco-Conscious Crafting: Sustainable Practices in Jewelry Production
As ESG compliance becomes a growing concern in global procurement, green manufacturing is no longer a “nice-to-have” but a core expectation. OEM/ODM manufacturers who prioritize eco-conscious production can secure long-term partnerships with forward-thinking brands.
Green Electroplating Technology
Traditional electroplating often uses cyanide-based solutions and heavy metals. Modern facilities are now shifting to trivalent chromium and non-toxic bath systems, which offer:
- Lower wastewater treatment requirements
- Reduced worker exposure to hazardous chemicals
- Compliance with REACH and RoHS directives
These methods are ideal for gold, rose gold, and silver finishes commonly applied to custom charm necklaces.
Waste Recycling and Closed-Loop Systems
Manufacturing stainless steel jewelry generates offcuts and polishing residues. State-of-the-art OEM partners employ recycling systems that:
- Recover up to 80% of stainless steel scrap for reuse
- Filter and recycle process water through multi-stage filtration
- Convert grinding sludge into secondary raw materials
This not only reduces environmental footprint but also brings down material costs—benefits that are directly passed on to B2B buyers.
Packaging and Carbon Footprint
Beyond production, attention is paid to sustainable packaging. Options like biodegradable mailers, recycled paper inserts, and QR-code-based digital manuals help cut paper waste. Some manufacturers even offer carbon accounting services to clients for full life-cycle transparency.
Case Studies: Integrating Tech and Sustainability in OEM/ODM Projects
Here are real-world examples that showcase how technology and green manufacturing elevate brand impact and customer satisfaction:
Case 1: North American Boutique Brand
Objective: Launch a series of custom flower-and-birthstone necklaces with eco-conscious packaging. Outcome: Leveraged 304 stainless steel and green electroplating for soft gold finishes. Used laser-cutting for fine flower detail. Included biodegradable gift boxes and digital warranty cards. Resulted in a 35% repeat order rate within 3 months.
Case 2: Japanese Wellness Company
Objective: Premium-grade necklaces with a saltwater-safe finish for coastal wear. Outcome: Used 316L stainless steel, hydraulic forming for domed flower bezels, and molybdenum-enhanced etching for symbolic wave patterns. Applied carbon-neutral production. Result: Secured contracts with five new distributors in Asia-Pacific.
Case 3: European Fashion Retailer
Objective: Fast-turnaround personalized necklaces with minimal environmental impact. Outcome: Deployed CNC-laser and closed-loop recycling processes for 1000+ SKUs monthly. Integrated QR code authentication for product traceability. Resulted in 20% lower returns and higher customer satisfaction scores.
Conclusion: Elevate Your Jewelry Line with Engineered Precision
The fusion of premium materials, cutting-edge technology, and sustainable practices is redefining what’s possible in the world of stainless steel birthstone necklaces. Whether you’re a startup launching a boutique collection or an established retailer scaling a private label, aligning with an OEM/ODM partner who delivers both technical and aesthetic excellence is the strategic advantage you need.
Ready to engineer beauty into your next jewelry line? Partner with us to create custom charm necklaces that resonate with your market, exceed quality expectations, and support your brand’s sustainability goals. Contact our OEM/ODM specialists today to explore your next jewelry innovation.