Innovation & Sustainability: Crafting Birthstone Flower Necklaces with Stainless Steel
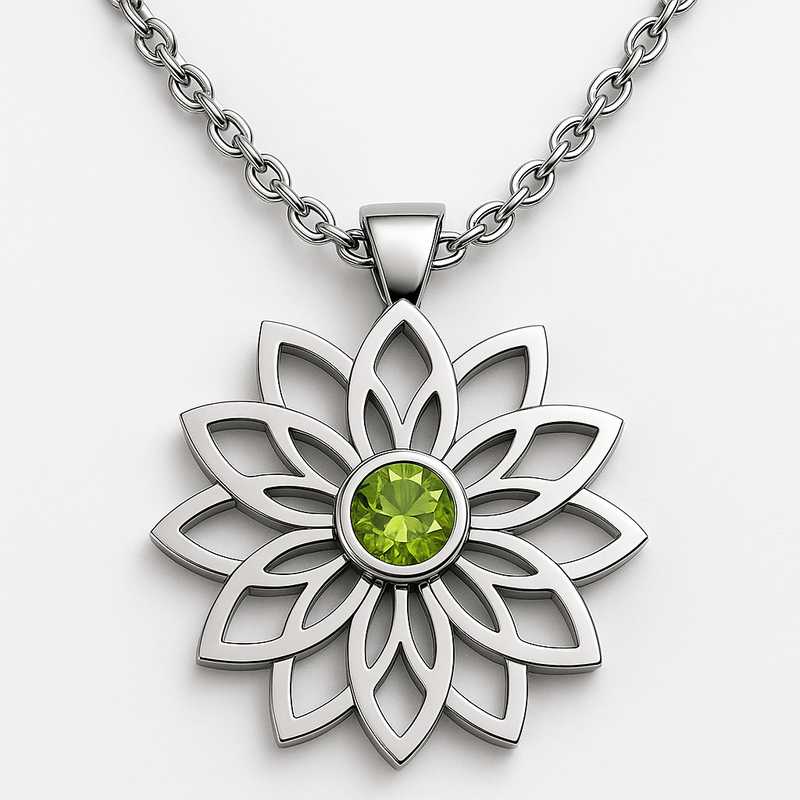
Comparing 304 vs. 316L Stainless Steel, Laser Cutting, Hydraulic Processing, and Green Production Methods
In the realm of custom jewelry manufacturing, B2B customers increasingly seek solutions that blend aesthetic appeal, technical reliability, and sustainability. The creation of birthstone flower necklaces using stainless steel is not only a celebration of personalization and elegance—it’s also a case study in innovative material selection and advanced production methods. For OEM/ODM clients in the stainless steel jewelry market, understanding the nuances between materials and manufacturing techniques is essential to making informed, competitive choices.
This special feature delves into the critical differences between 304 and 316L stainless steel, explores the precision enabled by laser cutting and hydraulic processing, and reveals how sustainable production practices—such as closed-loop waste systems and green electroplating—are shaping the next generation of environmentally responsible jewelry design.
Material Matters: 304 vs. 316L Stainless Steel in Jewelry Manufacturing
Stainless steel remains a cornerstone of modern jewelry design due to its durability, luster, and hypoallergenic properties. Among the various grades, 304 and 316L stainless steel are the two most common choices in premium birthstone flower charm necklaces. Each has distinct chemical compositions and performance attributes suited to different use cases.
304 Stainless Steel: The Standard Workhorse
Composed of approximately 18% chromium and 8% nickel, 304 stainless steel is well-known for its excellent formability and cost-efficiency. It performs admirably in non-corrosive environments and is ideal for indoor wear, especially in climates where sweat and humidity are minimal. However, prolonged exposure to saltwater or acidic environments may initiate surface oxidation or pitting.
316L Stainless Steel: The Superior Option for Longevity
316L stainless steel includes molybdenum, giving it superior resistance to corrosion and chemical damage. Its low carbon content (the “L” stands for “low carbon”) reduces susceptibility to intergranular corrosion. This makes 316L the preferred choice for high-end jewelry intended for daily wear, coastal markets, or tropical regions where moisture and salt are prevalent. In medical-grade applications, 316L’s hypoallergenic properties also enhance its appeal.
Application Comparison
- 304: Fashion-forward designs, short-term wearables, seasonal collections
- 316L: Premium lines, active lifestyles, high-moisture markets, heirloom pieces
Precision Engineering: Laser Cutting and Hydraulic Techniques
The intricate shapes and delicate patterns seen in birthstone flower necklaces require manufacturing technologies that guarantee both precision and repeatability. This is where laser cutting and hydraulic processing come into play.
Laser Cutting: Micron-Level Accuracy
Laser cutting is used to create floral outlines and setting slots for gemstone birthstones with a tolerance of less than 0.1mm. Using CAD files, OEM clients can quickly prototype and scale new designs with minimal material waste. The non-contact nature of lasers also reduces edge deformation, preserving the aesthetic clarity of intricate patterns like petals and vines.
Hydraulic Stamping: Controlled Force for Shaping
Hydraulic presses apply uniform pressure across stainless steel sheets to shape domes, bezels, and embossed motifs. This technique is especially beneficial in creating three-dimensional floral designs without introducing cracks or warping. Furthermore, programmable hydraulic systems allow for faster transitions between design molds, improving lead times for custom orders.
Use Case: Complex Layered Pendants
A recent OEM client requested a birth flower pendant with a two-layer structure—one for a brushed steel base and another for a mirror-polished overlay. Combining laser-cut profiles with hydraulic embossing enabled a visually striking result with strong structural integrity and excellent tactile quality.
Corrosion Patterns and Material Longevity
Understanding the long-term behavior of stainless steel in different environments is key to selecting the right alloy and finish. B2B clients must consider not only visual appeal but also lifecycle performance.
Common Corrosion Forms in Jewelry
- Pitting: Typically found in 304 stainless steel when exposed to chloride ions or skin acids
- Crevice Corrosion: Occurs in small gaps between joined parts, such as gem settings or pendant layers
- Surface Tarnishing: Though rare, poor surface passivation or exposure to harsh chemicals can dull finish
Finish and Surface Treatments
Electropolishing and passivation techniques can significantly improve corrosion resistance and surface brightness. Jewelry treated this way resists discoloration and retains its mirror finish longer, making it ideal for markets with high humidity or pollution.
Case Study: Marine-Inspired Designs
In a project targeting a beachwear accessory line, only 316L stainless steel with electropolished finishes passed the salt spray resistance test (ASTM B117) over 1000 hours. This confirmed its value for humid or coastal applications.
Green Jewelry Manufacturing: Towards a Sustainable Future
Today’s B2B buyers are not only interested in quality and aesthetics—they also demand environmentally responsible production. The stainless steel jewelry industry is rapidly evolving with eco-conscious practices that reduce carbon footprints and improve regulatory compliance.
Waste Recycling and Closed-Loop Systems
Scrap stainless steel from laser cutting and hydraulic processes is collected and recycled back into the material supply chain. By maintaining closed-loop systems, manufacturers achieve up to 95% material utilization rates, lowering both waste disposal costs and raw material expenses.
Green Electroplating Technology
Traditional electroplating can introduce hazardous chemicals into wastewater. Modern facilities are switching to cyanide-free and trivalent chromium plating solutions, which drastically reduce toxicity levels. Effluent treatment systems equipped with nanofiltration ensure that water discharged from plating tanks meets environmental safety standards.
Energy Optimization
Factories using servo-controlled hydraulic presses and fiber lasers consume less energy per unit produced. Solar panel installations on facility rooftops further offset emissions, while real-time energy monitoring allows for predictive maintenance and peak-load balancing.
OEM Best Practice: Transparency & Certification
Forward-thinking manufacturers provide clients with environmental compliance documents such as RoHS, REACH, and ISO 14001 certifications. This not only supports eco-conscious branding for retail partners but also facilitates entry into regulated markets in the EU and North America.
Conclusion: Turning Vision into Sustainable Craftsmanship
In an industry where precision, quality, and design innovation matter more than ever, the combination of advanced materials like 316L stainless steel and sustainable production techniques creates unmatched value. From corrosion-resistant birthstone flower necklaces to eco-friendly hydraulic stamping, OEM/ODM clients can now offer products that align with both market trends and ethical standards.
Whether you’re designing a new seasonal line or developing a long-term private label offering, partnering with a manufacturer that prioritizes technology, sustainability, and customization is the key to standing out. Contact us today to explore custom stainless steel jewelry solutions that are as forward-thinking as your brand.